
4-station
Injection Blow
Molding Machine
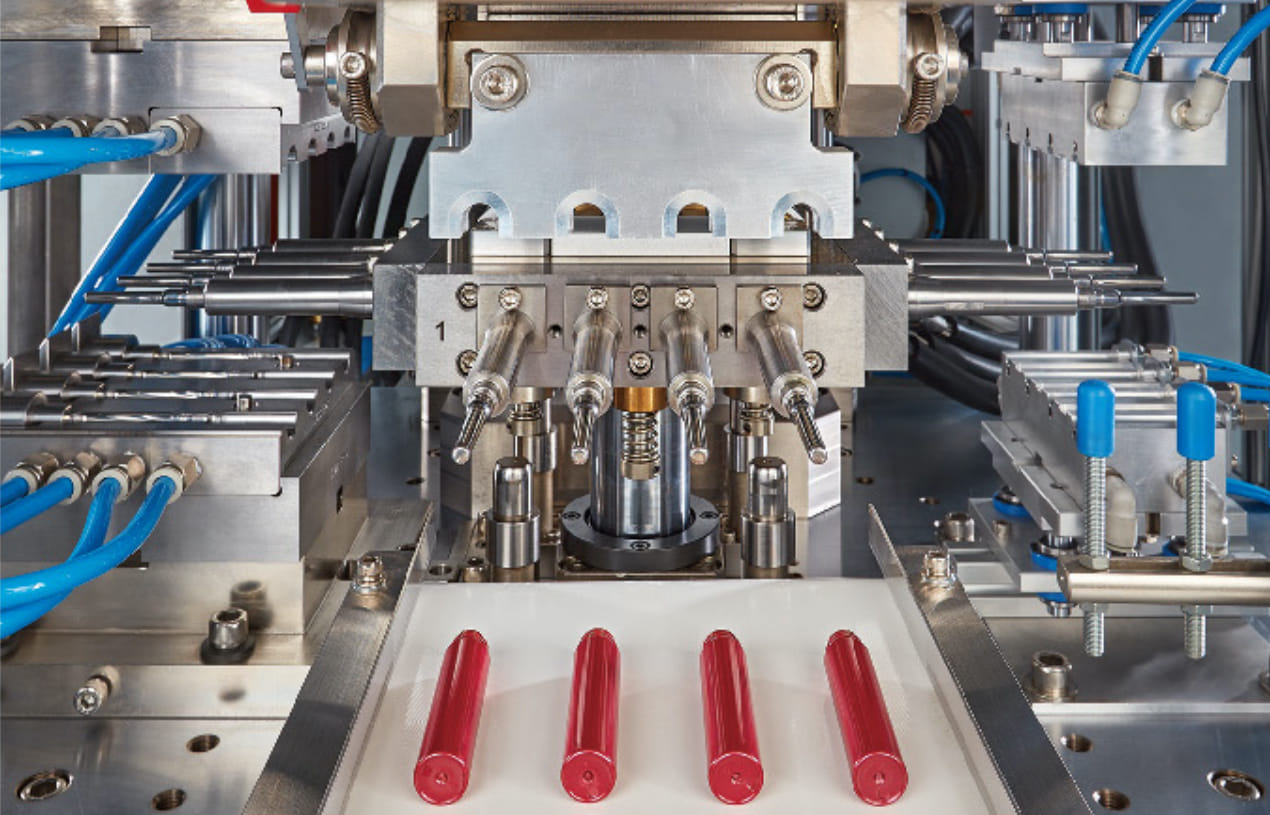
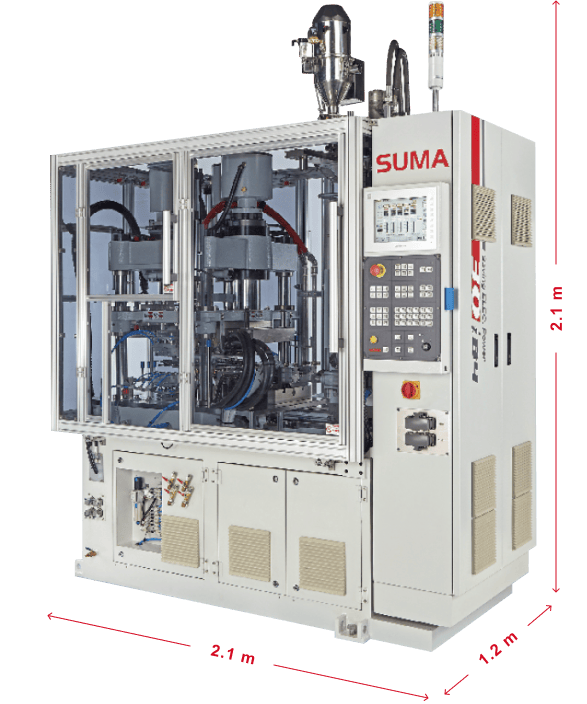
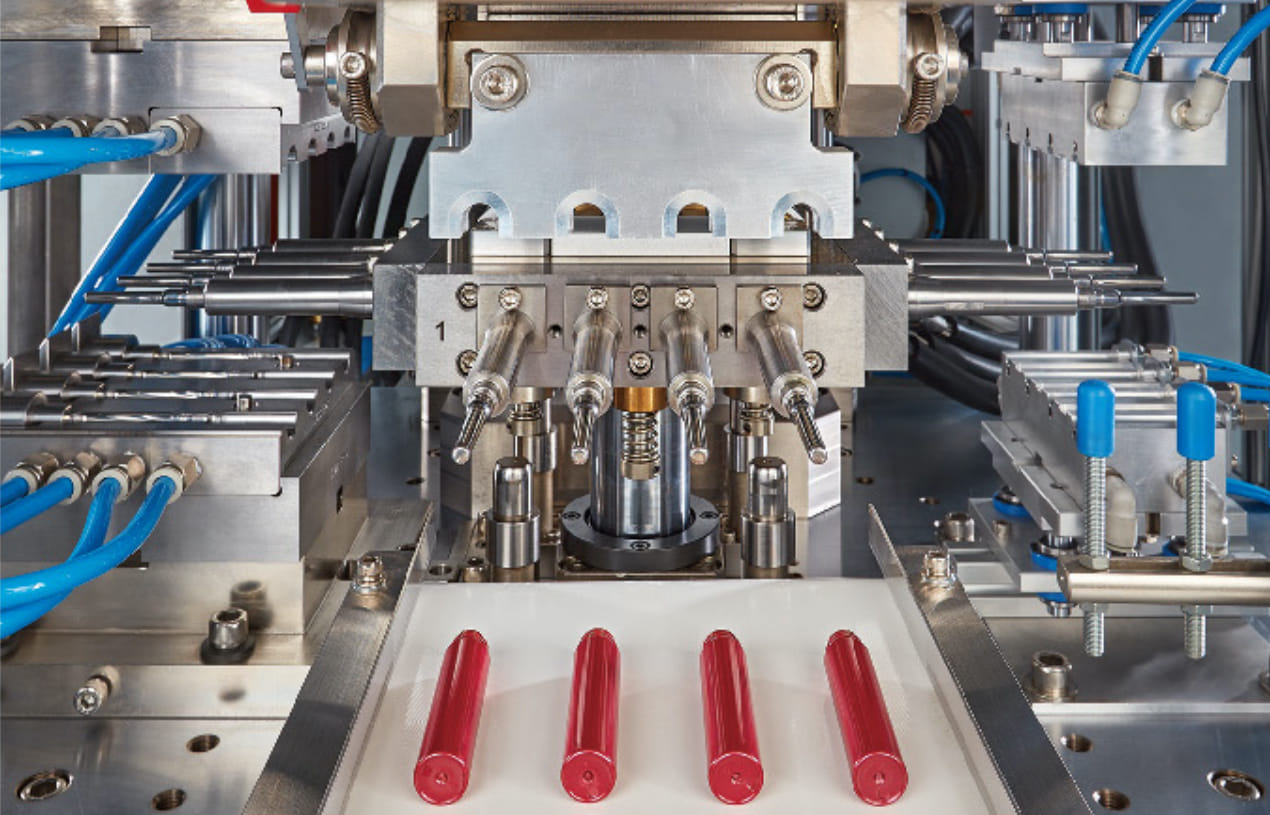
PROCESS
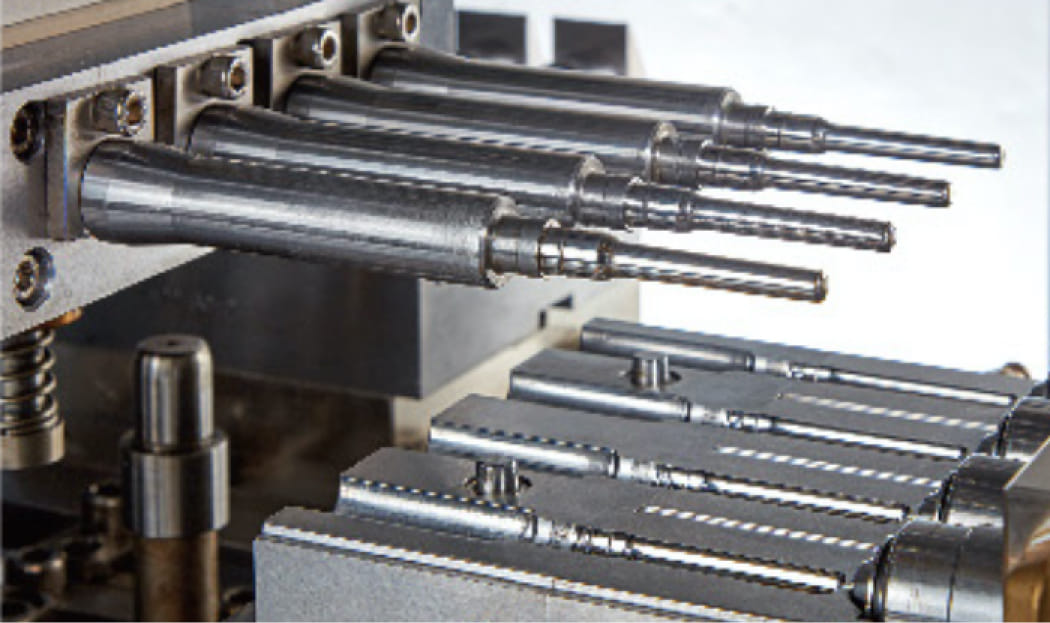
The material is injected into the preform cavities by injector and forming a parison with precise neck section.
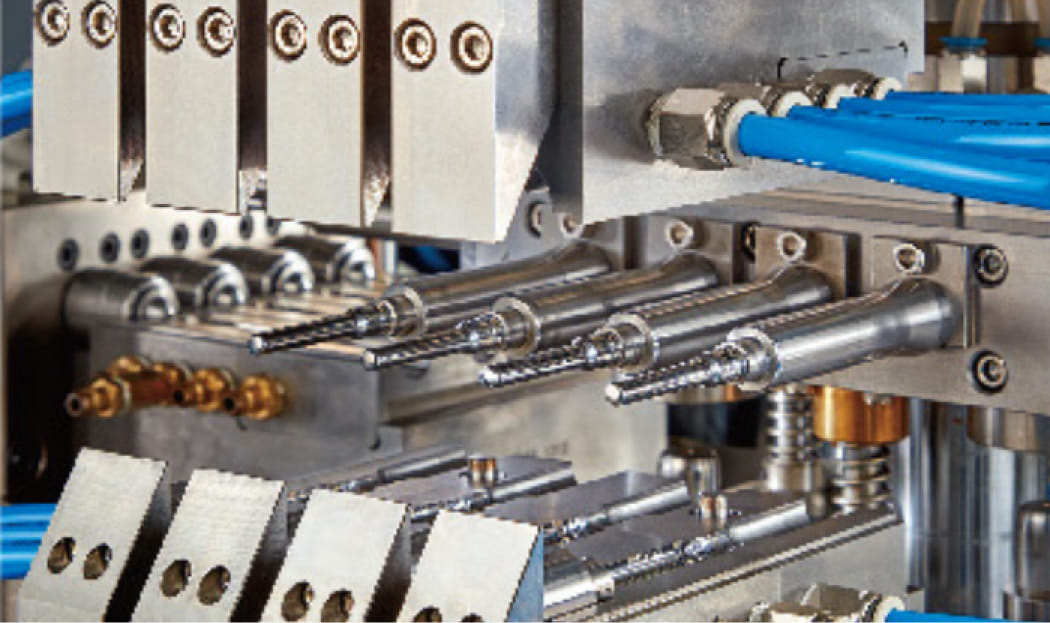
The turntable transfers the parisons to this step, the blowing, by rotates 90 degrees. Here, the parisons are blowing to form a container.
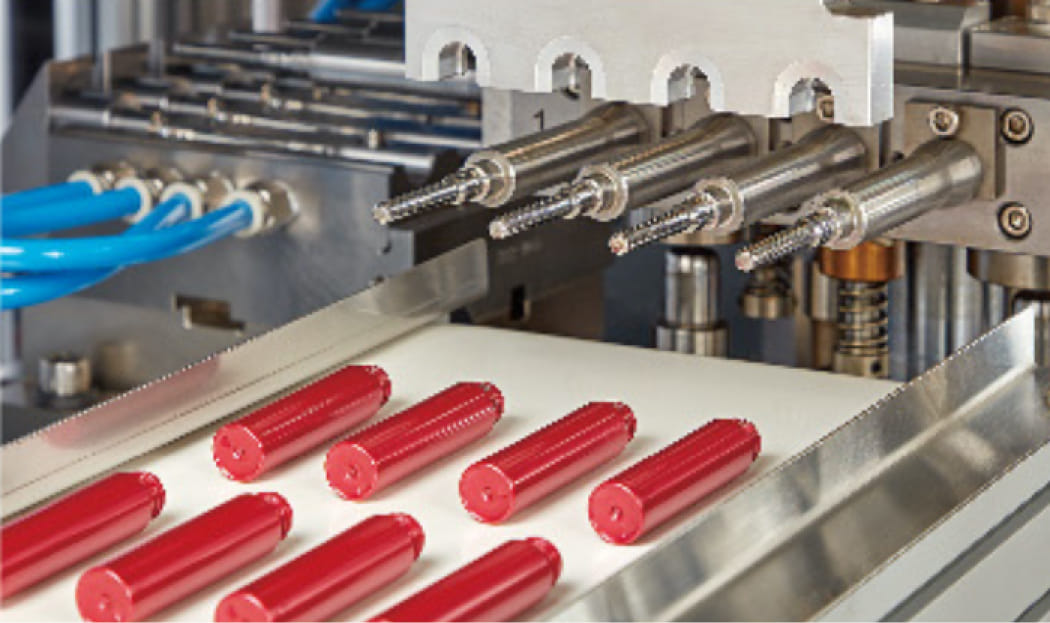
The turntable rotates again and transfers the shaped bottle to this step, stripping. The finished bottles are stripped by stripper and ejector.
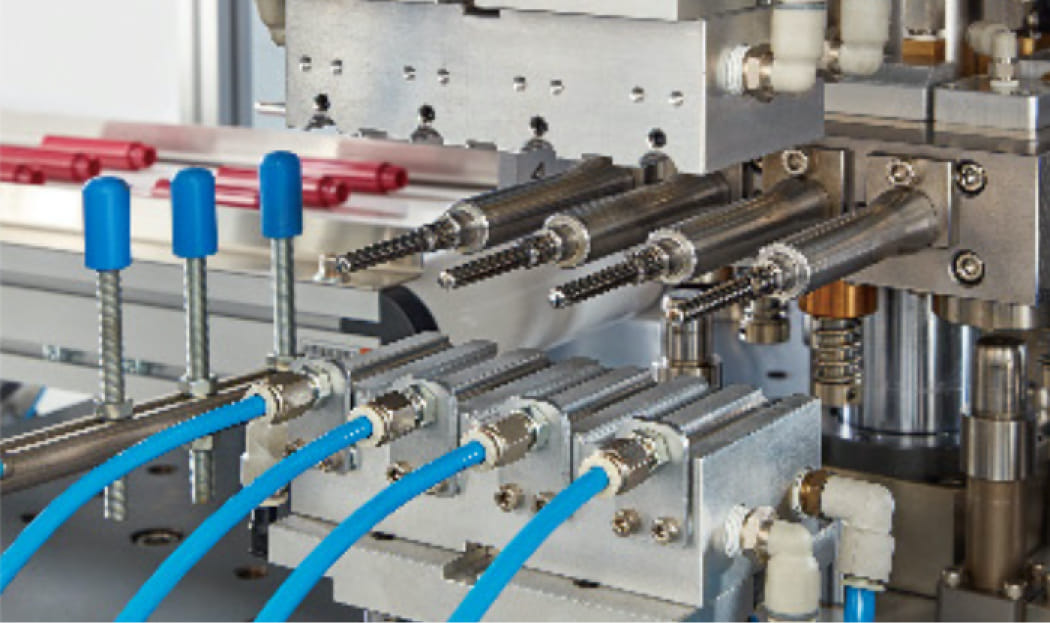
To adjust temperature of core rods depending varied bottle in this station. After adjustment, the finished bottles can be more stable and precise.
FEATURE
Space-efficient and modern design
The user interface is easy-to-learn.
Stable operation, energy saving and low noise.
Quick mold change and diversified packaging solutions.
Automatic producing and material saving. No need the process of deflashing and trimming.
Holding pressure free programmable in 3 steps. And 5 steps for each of injection and plasticizing.
-
Screw Diameter 30mm
-
Injection Volumn 95cm³/shot
-
Injection Stroke 135mm
-
Plasticizing Rate 6cm³/s
-
Screw L/D Ratio 22
-
Preform Clamp 200kN
-
Blow Mold Clamp 65kN
-
Press Stroke 130mm
-
Max. Die. Set 270x400mm
-
Trigger Bar 130mm
-
Dry Cycle Time 3sec
-
Oil Tank Capavity 65l
-
Low Compressed Air 6-10bar
-
High Compressed Air 20-40bar
-
Air Comsumption 300l/min
-
Power Supply 18kW
-
L x W x H 2.1x1.2x2.1m
-
Total Weight 3.5ton
BOTTLES
Cosmetics
Pharmaceutical
Personal Care
APPLICATIONS
PRODUCT DIMENSIONS

-
Cavity124
-
Center5038mm
-
Inside Neck Dia.6 - 50mm
-
Max. Body Dia.803525mm
-
Max. Height120120100mm
-
Max. Capacity1505015ml